- Drinking Water 2024 – Summary of the Chief Inspector’s report for drinking water in England
- Foreword
- Water supplies and testing
- Compliance with water quality standards
- Water quality events
- Asset health and service reservoir integrity
- Consumer contacts
- Water safety planning and risk assessment
- Perfluoroalkyl and polyfluoroalkyl substances (PFAS)
- Audit programme completed by the Inspectorate
- Enforcement, transformation and recommendations
- Lead in water
- Materials in contact with drinking water (Regulation 31)
- Security and Emergencies (SEMD)
- Network Information systems (NIS)
- Research publications
- Raw water data
- Whistleblowers
- Working with stakeholders
- Annex A – Number of tests carried out by companies
- Annex B – Compliance with standards
- Annex C – Compliance failures and events
Audit programme completed by the Inspectorate
In 2024 the Inspectorate carried out 77 audits, this is an increase over the 43 carried out in 2023 and highlights the Inspectorates increased focus given on water companies. The audits comprise of a mixture of onsite inspections, focused whole company audits and remote vertical audits.
The Inspectorate carries out series of thematic audits designed to access performance across the industry to look for areas of good and poor practice to disseminate the learning from these inspections widely across the industry to enable poorer performing companies to learn from examples of good practice.
Featured audits
Severn Trent Water – Bottle Store
Bottled water supplied by water companies is subject to the same regulations as water supplied by pipes or tankers and the storage. Additionally, bottled water must be treated like a food product considering the additional risks of the environment in which it is stored and the protection of the bottles if they are plastic as this could be affected by heat, sunlight, and rodents or other wildlife which may destroy or degrade the plastic or contaminate the bottle tops.
The Inspectorate conducted an unannounced audit of the bottled water kept at a Severn Trent Water storage facility on 27 September 2024. The storage facility was on first sight, unhygienic, and as a result the Inspectorate had no choice but to intervene to ensure that all the stored water was quarantined and destroyed to prevent its supply to consumers.
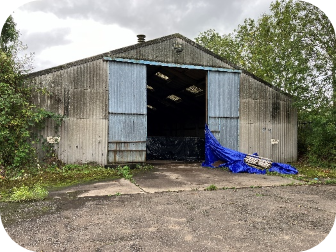
The storage facility was a dilapidated asbestos clad warehouse on a non-operational service reservoir site. It had been repurposed for bottled water storage in September 2021. The roof and walls were damaged, and skylights exposed the stored water to direct sunlight.
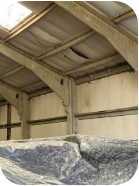
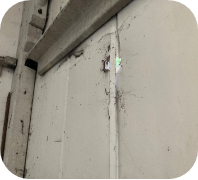
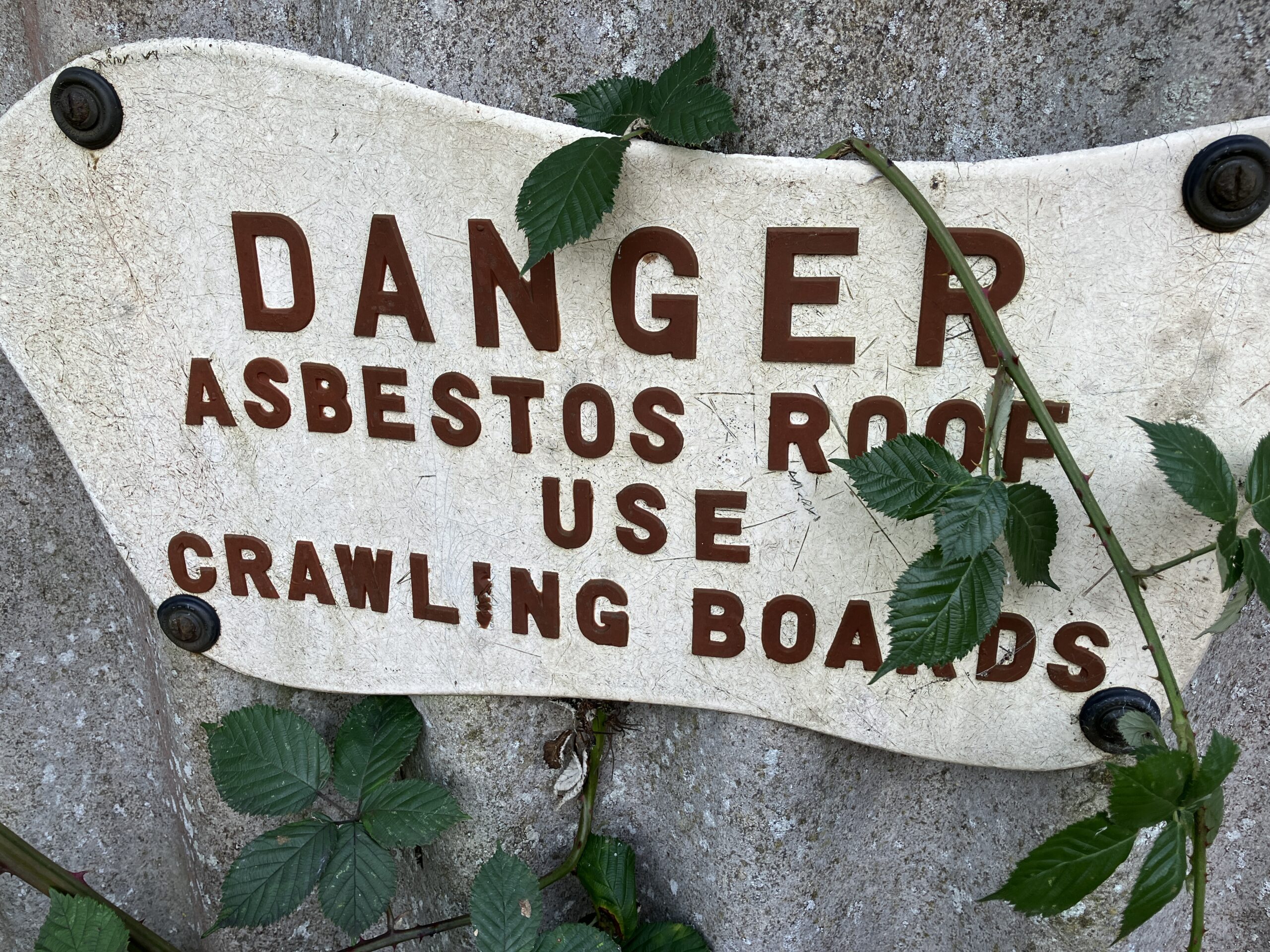
The doors to the facility were inoperable and at some stage an attempt had been made to place a tarpaulin cover over the entrance way. However, at the time of the audit the tarpaulin was pulled back from the doorway and held down by old pallets to prevent it from blowing in the wind. There is no evidence that this temporary cover was ever extended to the full height of the opening. The tarpaulin cover was dirty and covered in bird faeces.
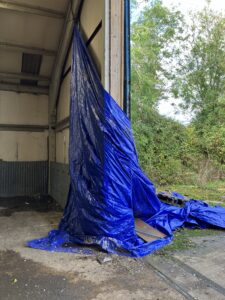
Severn Trent Water reported that concerns about the asbestos and leaking roof had been raised in December 2021 and that verbal reports of difficulties with operating the doors had been ongoing since late 2022, but the company were unable to provide any evidence of these concerns being raised, nor that any action was being taken to address the unsatisfactory storage conditions and exposure to the outside elements. Nevertheless, the exceptionally poor condition is evident as can be seen in the photo’s
Internally the facility was found to house approximately 300 pallets stored from wall to wall and covered in plastic sheeting. The top of the sheeting was covered in faecal material and the underside in contact with the pallets of bottles was dirty, suggesting it had been resting on the floor at some point.
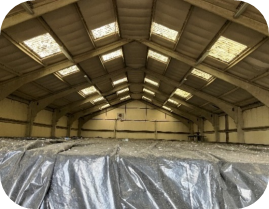
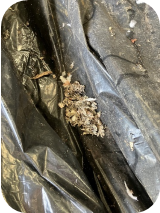
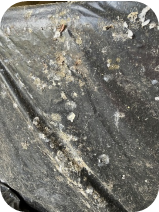
Many of the pallets of bottles still had the plastic covering from the supplier and this was seen to be dirty but remained intact. The Inspectorate discovered an open pallet with dirty bottles, from which a number had been taken and are likely to have been supplied to consumers. However, the company did not maintain records that could confirm where the missing bottles were sent.
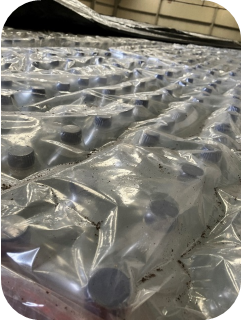
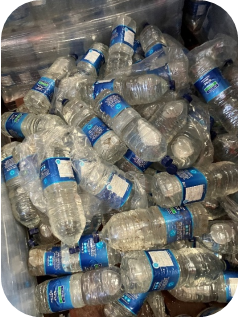
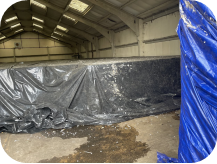
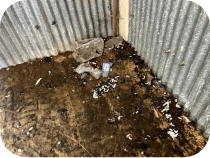
The floor of the warehouse was wet with the source either from the bottles or the environment that they were kept in. This could not be determined on the day. The floor was generally filthy and covered in faecal material.
Severn Trent Water reported that concerns with the facilities were raised internally on 5 September, about 3 weeks before the Inspectorate’s visit. The company had inspected the site on 13 September and had decided that the site was not to be used until further notice. The delay of over a week could have resulted in further deployments from the site in the interim. The company had taken no steps to visibly quarantine the stock at the time of the Inspectorate’s visit but subsequently erected a flimsy sign by the broken door to advise staff not to use the facility. The access was not even barriered off to prevent entry. This is not a drinking water quality first approach.
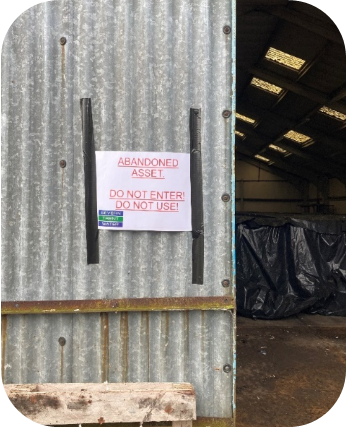
By storing the pallets from wall to wall, there was little opportunity for stock rotation and given the access limitations to the rear of the facility the Inspectorate were unable to confirm the age or batch numbers of the bottles stored at the rear of the warehouse. However, from the records available the warehouse was restocked in June 2024 following the deployment of 200 pallets of water to another company via a mutual aid agreement. The company were unable to confirm the batch numbers of the bottles supplied, the traceability of the stock was deficient. Evidence suggests that the bottled water had been stored for approximately 18 months, prior to the mutual aid request and most likely in the poor conditions observed in September 2024.
The company has a procedure that requires monthly sampling of stored bottled water, however for the batch deployed via mutual aid records for February and March 2024 only were available. The results were satisfactory for taste/ odour and routine microbiological parameters.
Following the audit the Inspectors concluded the lack of documented procedures, records and escalation of the issues, including the disregard for the presence of faecal material, poor environment of the storage facility, including inoperable doors and damaged asbestos storage facility, seriously undermines the Inspectorate’s confidence in the training and culture of the network response team responsible for the facility, and the inadequate response to quarantining and disposal of the poorly stored water perhaps raises doubt in the wider water quality culture within the company.
The complacency of the network response team and company to remediate the identified issues resulted in the deterioration of the facility with the conditions considered inadequate by the Inspectors for the storage of water intended for consumption and non-compliant with the industries own technical guidance note 11 concerning the storage and use of bottled water.
The Inspectorate took prompt action to serve a provisional enforcement order (PEO) on the company prohibiting the supply of any water from the store and to ensure its destruction. This is the first occurrence where such action has been necessary by the Inspectorate and is disappointing that this was necessary.
The company has discontinued using the facility with alternative third party storage locations now used for bottled water storage. Severn Trent Water also committed to further training of its staff with respect to management of bottled water in response to the provisional enforcement order.
The Inspectorate made recommendations for the company to improve procedures and implement an appropriate system of water hygiene audits for bottled water storage facilities.
A recommendation was also made for the company to consider the quality of bottled water supplies as part of its regulation 27 risk assessment and for this evidence of this in its reports.
There may be an assumption within the industry that bottled water is always stored hygienically. This incident shows that this is not always the case. The Inspectorate expects all companies to consider the water quality risks associated with bottled water supplies and ensure that it has appropriate training, procedures, and inspections in place to ensure action is taken to maintain hygienic supplies of bottled water as required. Similar audits may well be necessary across the industry to provide assurance that there are no similar situations.
Northumbrian water – Mosswood works audit
When a company notifies the inspectorate of an event which is considered sufficiently serious or there are repeat occurrences which may indicate a changing risk profile for a site, an audit may be carried out to determine the facts because drinking water is a critical societal service which can have a public health impact. One such occasion arose when there were two notifiable events in 2024 at Northumbrian Water’s Mosswood works following a power interruption. The lack of generator power led to treatment issues and sub-optimal clarification on two separate occasions in July and August 2024. The impact of a loss of power can be far reaching not just in the loss of supply but more critically the loss of some treatment processes but water is still in supply creating the risk of improper treated water reaching consumers.
Further to these events, an event was retrospectively notified, in August, due to a potential regulation 26 breach, that means preparing water sufficiently for disinfection following filter media replacement, and a return to service of the site. Retrospective notifications usually arise because a company either doesn’t think the threshold has been met for a notification, internal communications to water quality have not occurred so those responsible for making a notification don’t know, or the Inspectorate identifies information upon which a company is informed that they must notify.
As a third issue, the works had two coliform detections in regulatory samples in 2024. The company attributed the first detection in January 2024 to deficiencies with the sampling facilities, and the second in August 2024 to the condition of the contact tanks. Both contact tanks were inspected in 2023 and the company were given a recommendation to inspect them again following the first coliform detection in January 2024. ROV inspections were carried out in July 2024 where minor ingress was found in both tanks and some sediment deposition on the tank floor. The ingress in one tank was repaired, but investigations on the route of ingress in the other tank did not find the source. As a result, the company committed to installing a roof membrane over both tanks to mitigate the risk of ingress.
Given the ongoing concerns, the works was understandably subject to an audit by the Inspectorate in November 2024. In addition to the technical audit, a risk assessment and disinfection policy audit was carried out. The Inspectorate made recommendations around the filter monitoring and performance and hypochlorite dosing, specifically the chlorine residual and effective contact time to ensure disinfection is consistently achieved because of the long loop times and lack of chlorine residual monitoring. Furthermore, issues with works flow control, monitoring, and recirculation to the head of the works in contravention to the recommendations within the Badenoch and Bouchier expert report on Cryptosporidium were also found during the technical audit.
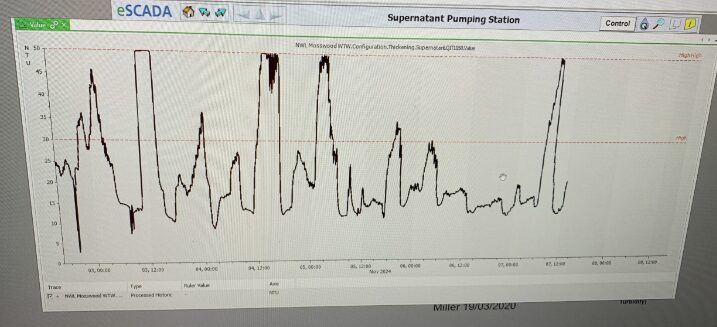
The risk assessment audit found good processes in place; however, the Inspectorate gave recommendations around the drinking water safety planning (DWSP) methodology. Further recommendations were made regarding the deficiencies identified around the DWSP training for the wider business and lack of internal auditing/verification processes for the DWSP.
The company’s disinfection policy was also reviewed as part of the audit, during which several deficiencies were identified. These included gaps in policy, training, insufficient alignment between the general policy and the site-specific disinfection policies (SSDP), lack of detail on disinfection approaches, discrepancies between SCADA Ct calculations and those outlined in the SSDP, and inconsistencies with relevant standards. As a result, the company was issued with a regulation 28(4) notice.
The audit identified multiple critical deficiencies across operational control, disinfection practices, and risk management. While some good processes were in place, the Inspectorate reminds water companies of the importance around filter management and flow monitoring, chlorine dosing and validation, correct operation of the recirculation to the head of the works, and DWSP implementation and training because together the risk incrementally increases. The Inspectorate expects water companies to establish a concise disinfection policy framework that is underpinned by robust scientific principles and can be adapted to site-specific requirements to protect public health.
Southern Water – Brede works audit
In addition to responsive audits, such as that exampled above, audits are also undertaken on a random basis to verify the general state of treatment works and supply systems which may otherwise not receive a visit or as an ongoing check on progress with any existing enforcement. Brede is one such example where the audit was to assess the works as part of the Inspectorate’s surface water treatment works audit programme for the third quarter of 2024, and to assess progress against legal instrument
Brede works is a surface water site treating water from Powdermill and Darwell surface water reservoirs and four interconnected wells. There were a number of recommendations surrounding critical treatment processes which were suboptimal. These were for the company to investigate and implement methods to ensure coagulant dose and DAF performance is optimised; to rectify the shortfall in media replacement which had not been corrected for six years; to investigate the settlement time following filter backwash which was recorded by the company to be 10 minutes long; to investigate the cause of the recurrent Clostridium perfringens detections and to develop robust short and long term solutions to reduce the risk of further detections. Further recommendations were made against filter performance, operation, inspections, primary filter roof repair and planned maintenance to clean the filter lauders. In the long term, the Inspectorate recommended replacement of the filters with a more appropriate and robust solution.
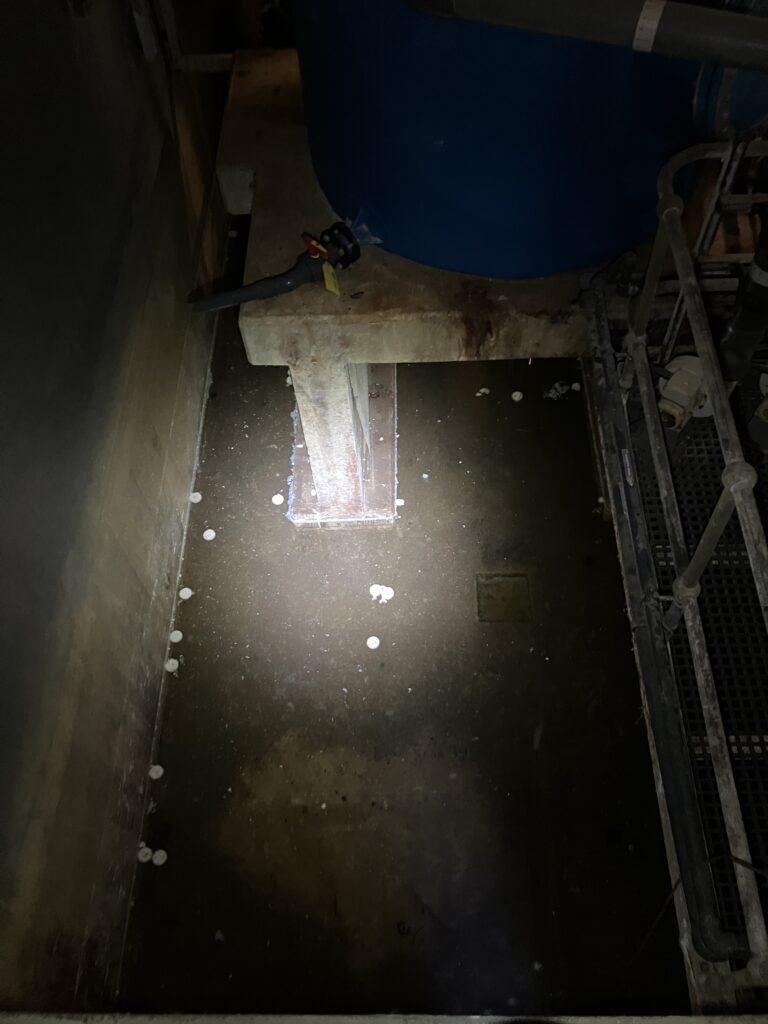
The Inspectorate found the works’ final water turbidity alarm allowed water to enter the final stage of disinfection for 30 seconds at a turbidity greater than 1 NTU before allowing the works to shut down. A recommendation was made to the company to introduce an appropriate alarm to allow works shutdown before the requirements of regulation 26 are breached at this site. The requirement to prepare water for disinfection by ensuring turbidity is below 1 NTU has been a requirement since 2007, it is therefore concerning that example of non-compliance with this requirement are still identified. The Inspectorate reminds all companies that water with a turbidity of greater than 1 NTU entering the final point of disinfection is in breach of the Regulations and all precautions must be taken to mitigate this scenario. Brede works is currently subject to an improvement notice, however the Inspectorate was minded to initiate further enforcement action following the audit.
South East water – Hazards Green works
Also in October 2024, the Inspectorate also visited South East Water’s Hazards Green works. The works is a surface water works located in East Sussex. Water is abstracted from the Wallers Haven River, Darwell Reservoir (which is managed by Southern Water) and an onsite well. South East Water list media depth checks for filters as a control measure on the company regulatory risk assessment however at Hazards Green works, it was apparent this was not taking place. This is a vital critical control measure to ensure filter performance to mitigate against Cryptosporidium breakthrough, highlighted by the Badenoch report of 1990. These finding should not still be identified by audit 35 later. The Inspectorate recommended the company reviews all sites to ensure that media depth checks are being completed at the required frequency and that the company update its Drinking Water Safety Plans to reflect the work it has identified to improve the control monitoring systems at the site.
Anglian water – Pitsford works
In November 2024, the Inspectorate carried out an audit at Anglian Water’s Pitsford works, which is a large surface water site located in Northampton, supplied by the River Nene, Pitsford Reservoir and Holcot, Walgrave and Scaldwell Brooks. The most significant challenge at the works is from pesticides, for which there is Granular Activated Carbon (GAC) treatment in place.
During the audit, Rapid Gravity Filter (RGF) 1 and 8 were found to be drained down and out of service for filter nozzle replacement. A subsequent data request following the audit found that RGF1 had been out of supply since April 2021 and RGF8 since May 2022 as the company had not been able to procure approved nozzles. The Inspectorate was critical that the status of the remaining six filters was being impacted by the company’s passivity in addressing the refurbishment issue and it was recommended that the company remediate the filter issues on site as a priority, so that the requirements of regulation 4 are not impacted in the future.
A further recommendation was made to review how the company’s maintenance systems highlighted instrument calibration dates in response to a turbidity instrument not receiving a timely two-year full loop calibration over a four-year period between 2020 and 2024.
United Utilities – Huntington and Sutton Hall works
In November 2024, the Inspectorate also audited United Utilities’ Huntington and Sutton Hall works, following a taste and odour event on the River Dee, which is the source water for both works.
The Inspectorate requested a Process Controller to be present during the two-day audit however, contrary to expectations, this did not occur. Water companies are under a primary duty to provide all such assistance and provide all such information as reasonably required, not to do so could be considered an offence. The Inspectorate reminds companies that it is always beneficial to have competent, trained and informed site operators present during a works audit to answer any questions regarding the day-to-day operation of the site.
Seven recommendations were made in total, with several under regulation 27, including to update the site risk assessments with site specific control measures; to develop a procedure and process to regularly verify the powdered activated carbon (PAC) dose at both Huntington and Sutton Hall works; to implement regular cleaning of all clarifiers and clarifier inlet channels at Huntington works due to the significant build-up of floc and sludge; to implement better control measures, to prevent contamination from buffers and reagents; and for regular maintenance and cleaning to be undertaken on the Actiflo streams at Sutton Hall works.
Enforcement has been initiated under regulation 28(4) at both sites for shortcomings in the PAC dosing, filtration maintenance and management, and contact tank inspection philosophy at Huntington works and for deficiencies in the PAC dosing system and filtration management at Sutton Hall works.
Affinity water – Kingsdown works
The Inspectorate audited Affinity Water’s Kingsdown works and found the company had not reported compliance data for the pesticides aldrin, dieldrin, heptachlor and heptachlor epoxide in recent years. A recommendation was given to the company to ensure compliance with the general provisions for monitoring in regard to the four aforementioned pesticides at this works and across the company’s estate. Another recommendation was made to ensure samples from Kingsdown works are always representative of water leaving the works as required by regulation 16, since the final water sampling tap had the possibility of being supplied by the network rather than the works, if the works was not pumping in to supply.
Further recommendations were made including the inclusion of sewer pumping stations within the catchment risk assessment; to review the company risk assessment records for risks associated with generators and transformers to be considered and updates to the regulation 28 report to be applied; to ensure risks associated with chlorate are controlled; and to hygienically seal an observation borehole located in close proximity to the site operational borehole.
The Inspectorate’s risk-based audit programme at works has emphasised many recurrent themes across the industry, particularly with regards to inadequate filter performance and maintenance, site-wide risk assessments and general site maintenance. Optimal filter performance and filtration are critical components of the production of a safe and high-quality water supply. However, at the majority of the sites audited, filter performance was found to be sub-optimal, with deficiencies observed in routine maintenance, inspection, cleaning and timely remedial interventions. Continuous risk assessment of treatment works should inform timely updates to company risk assessment reports with appropriate short-, medium- and long-term mitigation and control measures in place. However, this was also found to be inadequate at some of the works that had been audited. Site maintenance was also overlooked at almost all the works audited, in some cases for years, leaving assets to deteriorate.
The Inspectorate will always recommend or initiate enforcement to ensure compliance with the regulations n order to maintain wholesome water supplies to the public.