- Drinking Water 2024 – Summary of the Chief Inspector’s report for drinking water in Wales
- Foreword
- Water supplies and testing
- Compliance with standards
- Learning from compliance failures
- Learning from events
- Consumer contacts
- Asset health
- Water safety planning and risk assessment
- Raw water
- Poly and perfluoroalkyl substances (PFAS)
- Audit programme
- Recommendations
- Enforcement
- SEMD
- NIS
- Materials in contact with drinking water (Regulation 31)
- Research publications
- Whistleblowers
- Working with stakeholders
- Annex A – Number of tests carried out by companies
- Annex B – Compliance with standards
- Annex C – Compliance failures and events
Learning from compliance failures
Microbiological failures
In the spring of 2024 single coliforms were detected in final water samples taken at the Dŵr Cymru Welsh Water Builth and Bretton works. In both cases no definitive root causes were identified following reactive investigations. The contact tanks at both sites are single compartment tanks and resource constraints at the time prevented the timely reactive draining of these tanks for internal inspections. Pending these activities, remotely operated vehicle (ROV) inspections were conducted. Baffling in the Builth works contact tank prevented a survey of the whole tank. These examples demonstrate the need for access design and redundancy for all components that make up disinfection systems to allow for timely proactive and reactive maintenance.
Table 4. Microbiological tests – The number of tests performed and the number of tests not meeting the standard
Treatment works
Parameter | Current standard | Total number of tests | Number of tests not meeting the standard | Number of tests not meeting the standard by company |
---|---|---|---|---|
Clostridium perfringens (sulphite-reducing clostridia) (confirmed) | number/100 mL | 600 | 0 | – |
E. coli (confirmed) | number/100 mL | 12,108 | 0 | – |
Turbidity – indicator | NTU | 12,093 | 0 | – |
Total coliforms (confirmed) | number/100 mL | 12,108 | 2 | DWR (2) |
Service reservoirs
Parameter | Current standard | Total number of tests | Number of tests not meeting the standard | Number of tests not meeting the standard by company |
---|---|---|---|---|
E. coli (confirmed) | number/100 mL | 20,057 | 0 | – |
Total coliforms (confirmed) | number/100 mL | 20,057 | 12 | DWR (10) HDC (2) |
Consumers’ taps
Parameter | Current standard | Total number of tests | Number of tests not meeting the standard | Number of tests not meeting the standard by company |
---|---|---|---|---|
Coliform bacteria (indicator) | number/100 mL | 8,703 | 30 | DWR (26) HDC (4) |
E. coli (confirmed) | number/100 mL | 8,703 | 1 | DWR (1) |
Enterococci (confirmed) | number/100 mL | 753 | 0 | – |
Microbiological detections at works and service reservoirs
Table 5. Detection of E. coli and Enterococci at treatment works, service reservoirs and consumers’ taps
Company | E. coli in water leaving treatment works | E. coli in water leaving service reservoirs | E. coli at consumers’ taps | Enterococci at consumers’ taps |
---|---|---|---|---|
ALE | 0 – 0 | 0 – 0 | 0 – 12 | 0 – 4 |
DWR | 0 – 11,166 | 0 – 16,189 | 1 – 8,067 | 0 – 638 |
HDC | 0 – 942 | 0 – 3,868 | 0 – 624 | 0 – 111 |
Service reservoirs and treated water tanks analysis
In December 2023, Dŵr Cymru Welsh Water reported two coliforms in a regulatory sample taken at Croesor service reservoir. As part of the company’s investigation, it removed the reservoir from supply in January 2024 and carried out an internal inspection. Ingress was identified through an upstand during the flood test, and the company concluded that this was the likely cause of the coliform failure. The inspection also found that the internal upstands, walls, and floor were in poor condition and required full refurbishment. The reservoir was to remain out of supply until these remedial works had been completed, and satisfactory flood testing and commissioning sampling conducted.
The Inspectorate noted that the reservoir’s return to service was twice delayed due to pH exceedances in commissioning samples, although the cause and any investigation into it, was not explained by the company until the Inspectorate questioned it. The company initially attributed the high pH results in February 2024 (pH 9.7 and 9.3) to residual product in the newly lined reservoir. A further commissioning sample taken in March again failed due to high pH (pH 10.0). At this point the reservoir was internally inspected, and it was established that the cementitious product (initially unnamed), used to reline the walls of the reservoir had not cured properly. Only on request did the Inspectorate establish the product name and its regulation 31 reference. Documentation to evidence that the product was applied in accordance with its instructions for use (IFU) were requested. It was recommended that in future the company proactively provide more robust information in a timely manner (for the reasons given below), the company did not commit to improvements and as a result received a poor response score. Companies should be aware of the importance of proactively providing key information, supported by evidence, as soon as possible during an Inspectorate assessment. A piecemeal approach, responding only when prompted, may raise concerns about intentional concealment and can unnecessarily prolong the assessment process. In this case, the lack of transparency further diminished confidence in a company already under increased scrutiny due to its ongoing transformation.
Failure of a company (or its contractor) to apply or introduce a substance or product in accordance with regulation 31(1) is an offence under regulation 33(3)(a), although it is not an offence if the water that is exposed to the product is not supplied for consumption. In this case, no potential offence was committed as the reservoir was not in supply. The commissioning samples of the water acted to mitigate a near miss, illustrating how important the recommissioning process is in protecting consumers.
The Inspectorate concluded that whilst there was no absolute evidence that the contactor followed the IFU at the time the material was being applied to the interior reservoir walls, the steps of the procedure had been recorded (albeit lacking in detail). The critical question remained as to why the material did not cure as it should have done if the IFU was indeed followed, which the company claimed was the case. To address this, the company initiated an investigation while suspending the product from use for internal coatings until further notice.
Croesor service reservoir remained out of service while refurbishment of the walls was completed using an alternative regulation 31 approved product. It should be noted that the highest pH result returned on a commissioning sample at this reservoir (pH >10) was taken in April following this recoating with the second product. This demonstrates that potential pH issues following the application of cementitious coatings is not limited to an individual product, rather cement-based products more generally.
When cementitious products are tested for use in contact with water intended for human consumption (BS 6920) the testing is preceded by initial soaking periods. These soaking periods act to draw out the compounds in cement which are liable to leach out and raise the pH of the water in contact with the cement. In this case the company investigation concluded that the elevated pH detected was due to a combination of aggressive feed water (when compared to the water used to test the product according to BS 6920) and a greater surface area to volume ratio in the reservoir compared to test conditions. Hence, companies should consider the surface area to volume ratio when applying coatings to the internal parts of tanks, and the initial tendency for cementitious products to raise the pH of water in contact with the product.
The company, following prompting from the Inspectorate, undertook an internal audit to ensure that their contractors have procedures in place to ensure regulation 31 approved products are used in accordance with manufacturers’ instructions. A further technical review by a third-party consultancy which included queries over the curing time and the surface area to volume ratio was also conducted.
In conclusion, the company’s commissioning procedure following the application of both cementitious products was able to both prevent water with a high pH from going into supply. In addition, the curing issues experienced with the first product were only identified once the service reservoir had been drained down after high pH results. Companies are reminded to state the reason for any delay in the return-to-service of an asset and to include an evidence-based investigation for any parameter breach of a commissioning sample as part of its ongoing reporting duties. Companies are also reminded that they are ultimately responsible for work conducted by contractors on their behalf, and the record keeping and communication between the company and contractors may be called upon following a potential breach of the Regulations. Regular scheduled company audits of their contractors should reveal potential deficiencies in contractor procedures, processes and record keeping.
There have been 12 bacteriological compliance failures at Dŵr Cymru Welsh Water works and service reservoirs in Wales in 2024. The majority of the breaches were associated with ingress into service reservoirs. While this is an improvement on the previous year, the company is yet to fully realise the benefits of the service reservoir work delivered against its regulation 28 notice since it was served in April 2022. To fully realise the benefits, the company must establish a suitable base-level of inspection and maintenance, based on risk, to achieve and maintain an overall reduction in risk.
On 30 October 2024 a compliance sample was taken by Dŵr Cymru Welsh Water at Newlands service reservoir which contained one total coliform per 100 mL. The ingress of roots (Image 1: below, top left) and a worm (Image 2: below, top right) through the gaps in the wall to roof joints was identified during a reactive internal inspection of compartment one on 13 November 2024, which is a brickwork tank with an aluminium roof (Image 3: below), with no defects identified in compartment 2 which is of a concrete construction. These defects in compartment 1 were concluded as the most likely root cause for the breach. Similar observations of leaking roof joints during flood testing were made during an internal inspection of compartment 1 in September 2020. Whilst repairs were carried out and the tank reinspected with a passing flood test in November 2020 the microbiological compliance breach in October 2024 demonstrates the importance of risk assessment in defining appropriate maintenance programmes. Where the construction, condition and relative risks associated with separate assets on a single site varies this should also be considered when designing these programmes.
Images 1, 2 and 3 Newlands service reservoir
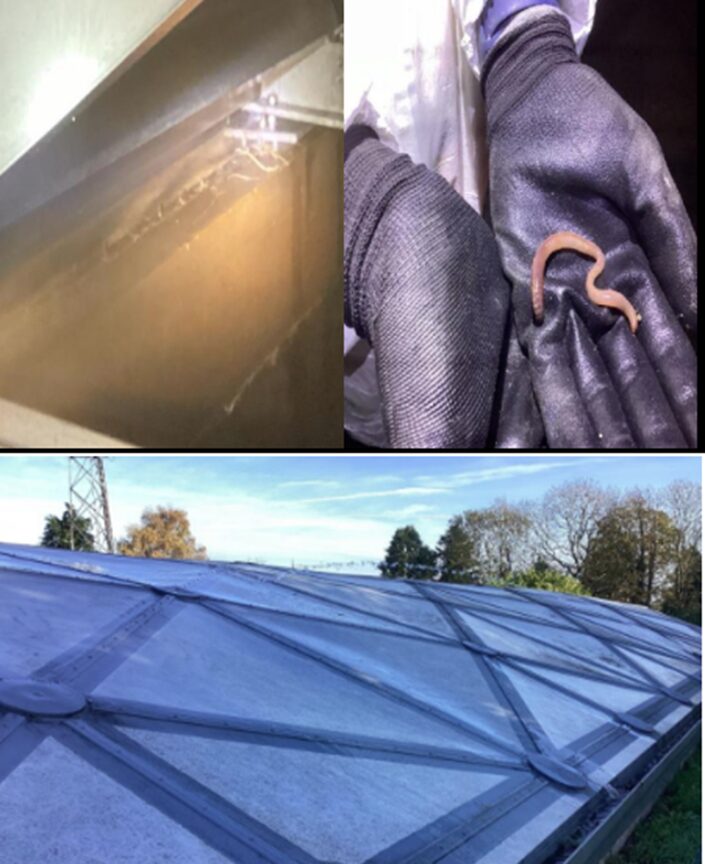
A sample taken by Hafren Dyfrdwy at Cefn Twlch service reservoir on 5 April 2024 contained a single coliform per 100 mL. The reactive investigation highlighted defects with the sampling facilities including a poor sampling environment, with the tap housed in a roadside cabinet with overhanging trees, and inadequate drainage. The tapping point chamber was also found to be flooded providing opportunity for ingress. The company stated that the sampling facilities did not conform to the existing design standards, and in response, installed a new sampling kiosk prior to the return of the reservoir to supply and initiated additional annual reservoir sample facility audits to be conducted by local operatives. Companies are reminded that sampling facilities should meet the requirements of regulation 16 with respect to ensuring appropriate, hygienic sampling facilities are available for obtaining representative compliance samples. Such facilities should conform to companies’ own standards and deviation from said standards should be noted and remediated following observation through routine site visits, inspections and other risk assessment processes.
In Figure 7, while the lower figures in 2020 and 2021 can largely be attributed to reduced sampling during the pandemic, the overall trend has continued to rise year on year since 2018. Of the 31 breaches recorded in 2024, 26 were deemed unlikely to recur, with 20 of these linked to the domestic distribution system.
This upward trend may be influenced by the replacement of older taps with simple spouts by modern designs incorporating additional internal features, such as aerators, which can promote microbial growth. Swabbing taps before sampling could help identify them as potential sources of contamination.
For the remaining five breaches, the cause was not determined. However, company responses have continued to improve, and it is positive to note that no recommendations were issued for these breaches in 2024.
Chemical and physical parameters
Table 6. The number of tests performed and the number of tests not meeting the standard
Parameter | Units | Total number of tests | Number of tests not meeting the standard | Number of tests not meeting the standard per company |
---|---|---|---|---|
Colour |
mg/L Pt/Co |
3,187 |
1 |
HDC(1) |
Odour |
Dilution number at 25°C |
3,183 |
4 | DWR(3) HDC(1) |
Taste (quantitative) |
Dilution number at 25°C |
3,183 |
8 |
DWR(7) HDC(1) |
Hydrogen ion (pH) – indicator – zone |
pH Value |
3,186 |
0 | |
Sulphate |
mg/L SO₄ |
462 |
0 | |
Sodium (total) |
mg/L Na |
755 |
0 | |
Nitrate (total) |
mg/L NO₃ |
756 |
0 | |
Nitrite – consumers taps |
mg/L NO₂ |
755 |
0 | |
Ammonium (zone) |
mg/L NH₄ |
921 |
0 | |
Aluminium (total) |
µg/L Al |
3,152 |
0 | |
Iron (total) |
µg/L Fe |
3,155 |
13 | DWR(12) HDC(1) |
Manganese (total) |
µg/L Mn |
3,156 |
1 |
DWR(1) |
Copper (total) |
mg/L Cu |
755 |
0 | |
Fluoride (total) |
mg/L F |
462 |
0 | |
Arsenic (total) |
µg/L As |
755 |
0 | |
Cadmium (total) |
µg/L Cd |
754 |
0 | |
Cyanide (total) |
µg/L CN |
462 |
0 | |
Chromium (total) |
µg/L Cr |
755 |
0 | |
Mercury (total) |
µg/L Hg |
465 |
0 | |
Nickel (total) |
µg/L Ni |
755 |
2 |
DWR(1) HDC(1) |
Lead (10) |
µg/L Pb |
755 |
1 |
DWR(1) |
Antimony |
µg/L Sb |
755 |
0 | |
Selenium (total) |
µg/L Se |
755 |
0 | |
Pesticides (total by calculation) |
µg/L |
704 |
0 | |
Polycyclic aromatic hydrocarbons (total by calculation) |
µg/L |
727 |
0 | |
Residual disinfectant – free |
mg/L |
8,746 |
0 | |
Residual disinfectant – total |
mg/L |
8,121 |
0 | |
Electrical conductivity |
µS/cm at 20°C |
2,959 |
0 | |
Boron |
mg/L B |
455 |
0 | |
Benzo[a]Pyrene (total) |
µg/L |
761 |
0 | |
Tetrachloromethane (total) |
µg/L |
464 |
0 | |
Trichloroethene & Tetrachloroethene – sum of 2 substances (total by calculation) |
µg/L |
465 |
0 | |
Trihalomethanes (total by calculation) |
µg/L |
757 |
0 | |
1,2-Dichloroethane (total) |
µg/L |
466 |
0 | |
Benzene (total) |
µg/L |
466 |
0 | |
Bromate |
µg/L BrO₃ |
583 |
0 | |
Gross alpha |
Bq/L |
1 |
0 | |
Gross beta |
Bq/L |
1 |
0 | |
Tritium |
Bq/L |
1 |
0 |
Lead
Lead is a toxic metal that can dissolve into drinking water when it comes into contact with lead pipes. Consumers are largely protected from exposure through phosphate dosing, a widely used treatment across many zones in Wales that reduces plumbosolvency. This approach is one of the key reasons why few, if any, consumer tap samples fail the lead standard each year. Additionally, the relatively low number of required lead tests under the Regulations contributes to this outcome.
As part of Price Review 2024, companies submitted lead reduction strategies with a target of achieving lead-free water supply zones by 2050. However, current plans will not meet this goal, therefore there is an expectation that strategies will accelerate in subsequent AMPs.
The single failure in the Wales area in 2024 was attributed to a lead communication pipe within a phosphate dosed zone. This pipe was replaced with MDPE and the consumer was given flushing advice due to lead solder on their private plumbing.
Taste and odour
There were 12 taste and odour breaches in Wales in 2024 which is an increase from 10 in 2023 which can be seen in Figure 8. In Dŵr Cymru Welsh Water’s Bontgoch zone, an investigation is being undertaken by Atkins Realis in response to a building history of taste and odour failures. It also experienced three taste cancellations, one of which was due to particulates present in the sample in relation to a burst main event, another being due to discolouration which required further investigation to prove as transient. Figure 8 also highlights a rise in failures in 2019 following the introduction of Information Letter 02/2022, which mandated companies to report cancelled taste tests as failures. The number of failures declined in 2020 and 2021, attributed to adjustments in sampling locations during the pandemic. Whilst the last three years have similar numbers of taste and odour failures, the taste and odour section further on in this report describes an increasing rate of contacts regarding taste and odour across Wales across the past few years.
In June 2024 Dŵr Cymru Welsh Water cancelled taste analysis on a sample following the detection of a spider in the sample bottle (Images 4 and 5 below). This follows a similar occurrence in October 2023, in which a fruit fly was found in a sample bottle. In both cases the company reported the taste cancellation as a regulatory compliance breach as required by Information Letter 02/2022. A recommendation was made for the company to review and update their sampling and bottle storage policy/procedures to mitigate the potential for the ingress of insects during sampling, with the company implementing additional contamination checks as a result.
Images 4 and 5 Spider in sample bottle
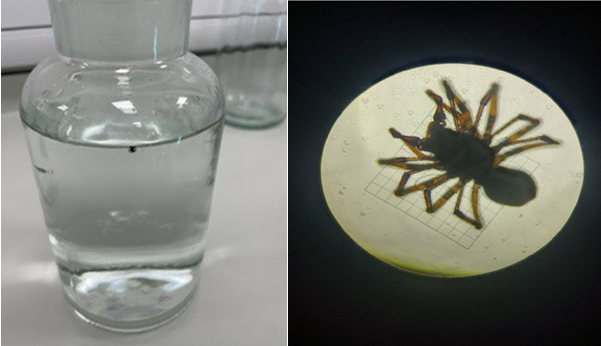
Iron
Dŵr Cymru Welsh Water is optimising treatment processes at Talybont works for multiple drivers, one of which is the apparent increase in algal activity in the supplying reservoir. One failure in the Abergavenny zone was attributed to this issue. There is a rolling GAC regeneration programme due for completion at the end of 2025 which should improve removal efficacy for taste and odour compounds. Improvements at Talybont works are formalised in a regulation 28 notice.
Distribution iron breaches continue across Wales with these discussed in 10 assessment letters during 2024. Given the association with the ongoing poor performance in other discolouration metrics in Wales this trend is a cause for concern. In some cases, the existing legal instruments in place have provided assurance that network interventions will mitigate recurrence in the short term. However, a large number of breaches were associated with the impact of mains in poor condition, local flow dynamics and other legacy conditions which have been mitigated through reactive flushing programmes. The impact of these programmes has in some cases proved detrimental rather than beneficial to local water quality and recommendations have been made to ensure appropriate monitoring and control of this impact. In some instances, flushing has been conducted prior to reactive/investigatory sampling and so investigations into root causes have been compromised. The trailing of Welsh companies behind industry targets suggests that current investment and delivery of agreed projects is not delivering the required changes at a sufficient pace.
In January 2024, a sample taken in a Hafren Dyfrdwy concessionary supply zone breached the regulatory standard for colour. Properties in this zone are supplied by individual private sources and are subject to a permanent boil water notice (BWN). A regulation 28(4) notice was served on 8 November 2023 which requires all properties in this zone to be connected to the mains water network by 31 March 2026. The BWN is unlikely to mitigate the risk from wholesomeness aesthetic breaches such as colour. A recommendation was therefore made that precautionary do-not-drink advice be issued following breaches of non-microbiological parameters in the concessionary supplies zone.
There were two nickel failures in Wales in 2024. Both were attributed to new chrome taps, however the failure in Hafren Dyfrdwy’s legacy zone was from a sample taken from a little-used utility room tap. A suggestion was made to review the tap selection procedure to ensure that samples taken are representative of the incoming supply.